1.はじめに
半導体製造では、プロセスごとに厳格な環境管理が求められ、その中で石英ガラス製品は欠かせない役割を果たしています。ウェーハの処理、拡散、エッチング、洗浄など、各工程で使用される石英製品は、高い耐熱性や化学的安定性が求められます。しかし、石英ガラスは加工が難しく、高いコストが発生する素材のひとつです。
特に半導体業界では、「精密な設計が必要」と考えるあまり、実際には不要な高精度を指定してしまい、結果としてコストが膨らんでしまうケースが多く見受けられます。
本記事では、半導体業界の皆様が石英ガラス製品を発注する際に、どのようにしてコストを最適化できるのかを、具体的な方法とともに詳しく解説していきます。石英ガラス加工の基本構造を理解し、発注時に適切な仕様を選定することで、大幅なコスト削減が可能になります。
具体的には、石英ガラス加工におけるコスト削減のための設計段階の工夫から、最新技術の活用、プロセスの最適化まで、実践的なアイデアを幅広くご紹介します。
特に半導体製造や研究に関わり石英製品をお使いの方、これから使おうと検討されている方、価格を少しでも安くしたい方など参考になる内容ですのでぜひ最後までお読みください。
2.石英ガラス製品のコスト構造
石英ガラス製品のコスト構造はそもそもどのようになっているのでしょうか?
基本的には大きく2つからなっています。一つは「素材(材料)」ともう一つは「加工」です。
➀素材コスト
石英ガラスには、溶融石英、合成石英、高純度石英など複数の種類があります。特に半導体製造で使用される石英は、高純度のものが求められるため、一般的なガラスに比べて高価です。さらに、素材の調達状況や市場価格の変動にも影響されます。
②加工コスト
石英ガラスは、一般的なガラスよりも硬く脆いため、精密加工に高い技術と時間が必要 です。加工の種類としては、以下のものが挙げられます。
- 耐熱• 切断
ダイヤモンドブレードなどによる加工 - 研磨
表面粗さの調整 - 穴あけ・溝加工
特殊工具を使用 - 接合
溶接や接着技術 - 洗浄・アニール処理
純度の維持・歪み除去
これらの工程が増えるほど、加工コストが高騰します。したがって、必要な仕様を適切に選定し、無駄な加工を省くことが、コスト削減のカギとなります。
弊社は石英ガラスを「加工」をして製品にするのが仕事ですので「素材(材料)については材料メーカーから仕入れる事になり、その材料を「加工」する事でお客様の希望される形(製品)に仕上げていく事になります。
本ブログではこの「加工」の部分を中心にいかにコストを削減できるかを考えていきたいと思います。
3.発注側(お客様/半導体製造関連企業様)でできるコスト低減の具体的方法の提案
発注側でできる石英加工品のコスト低減の方法としては次のような事が考えられます。
- 必要な精度を明確にする
- 形状設計をシンプルにする
- 標準規格品の活用を検討する
- 加工可能性を考慮した設計をおこなう
- 注文ロットを大きくする
- 材料の選定を慎重におこなう
- リードタイムに余裕を持たせる
- 試作品を作成してから量産する
- 加工業者と早い段階で相談する
- 長期的なパートナーシップを築く
これらについて説明していきます。
A.必要な精度を明確にする
加工精度が高くなるとどうしてもコストは上昇します。必要以上の公差や表面粗さなどが本当に必要なのかを良く検討して頂ければと思います。※図1、2,3参照
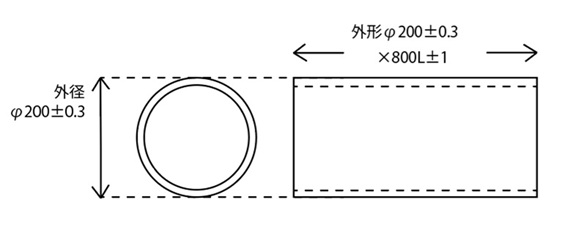
図1・・・本当にチューブ全体にわたって外径100±0.3が必要ですか?
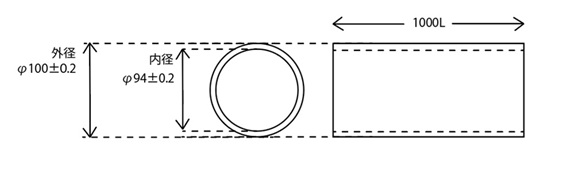
図2・・・本当に内外径の両方に精度が必要ですか?どちらか(外径、内径)一方の公差で使用できませんか?
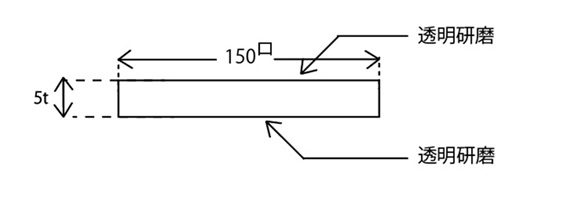
図3・・・板は透明の研磨が必要ですか?砂目でも大丈夫ではないですか?
半導体製造での具体的事例①・・・不要な公差の削減
半導体製造装置のチャンバー内で使用する石英ガラス部品について、±0.1mmの厳しい公差を指定していたが、実際には±0.5mmでも問題なく機能することが分かり、公差を緩和することで加工時間が短縮され、コストが5% ~10%削減。
B.形状設計をシンプルにする
必要以上に複雑な形状や不要な機能を含む設計は、加工時間とコストを増大させますのでできる限りシンプルな形状にして下さい。
半導体製造での具体的事例②・・・角Rの最適化
石英ガラスの角部にR0.2の精密加工を求めていたが、実際にはR1.0でも機能に影響がないことが分かり、加工の難易度が下がり破損リスクも軽減し、製造コストが数%削減。
C.標準規格品の活用を検討する
特殊な形状やサイズではなく、既存の標準企画品を活用できないか検討することで加工時間や費用を削減することが可能になります。
これはチューブ(管)の規格品の寸法の一部です。チューブ(管)は様々な規格品(内径、外径、長さ)の物がありますのでこれらを使用することで径の修正の必要が不要になったり、僅かな修正で済むことがあります。(※注意 規格の一例)
半導体製造での具体的事例③・・・規格チューブの活用
拡散炉装置内で使用する外径φ250mmの石英管を特注で加工していたが、既存の規格チューブ(φ254mm)を利用することで、外径加工を省略でき、コストを10%~20%削減。
D.加工可能性を考慮した設計をおこなう
石英ガラスは硬くて脆いため特定の加工、例えば細かな穴あけ、薄い肉厚や薄い板物などの加工は歩留まりが低下(破損のリスクが高くなる)するため価格が高くなりやすいです。
半導体製造での具体的事例④・・・小径穴の最適化
ガスの流れが重要な装置でφ0.2mmの微細穴を多数加工していたが、一部の穴径をφ0.5mmに変更することで、加工時間の短縮と歩留まり向上により、コストを削減。
E.注文ロットを大きくする
小口のロットより大口のロットの注文の方が単価は下がる場合があります。可能であれば複数回の注文を纏めて発注することをご検討下さい。
半導体製造での具体的事例⑤・・・半年分の発注でコストダウン
装置内で使用しエッチングにより消耗する部品を毎月30個ずつ発注していたが、半年分(180個)まとめて発注することで材料の調達コストが下がり、単価を削減。
F.材料の選定を慎重におこなう
石英の材料は様々ありますので用途に応じて最適な石英ガラスの種類を選定することでコスト低減ができることがございます。高純度が不要な用途もありますのでご検討下さい。
これは一般的な溶融石英と高純度の溶融石英と合成石英の純度表です。特に高純度な石英や合成石英などを使わなくても一般的な石英で十分使用できる製品が多いです。
半導体製造での具体的事例⑥・・・標準溶融石英への変更
研究開発時には合成石英を使用していたが、純度の要件を見直した結果、一般的な高純度溶融石英で十分であることが分かり、材料費で30%~40%削減。
G.リードタイムに余裕を持たせる
どうしても短納期で注文しなければならない時もあるかと思いますが、工場によっては割増料金が発生してしまうケースもありますので余裕を持ったリードタイムでご発注下さい。
半導体製造での具体的事例➆・・・余裕を持った在庫確保
加工業者と相談し、長納期対応でも問題ない部品はまとめて発注し、ストックすることで工場の生産計画が余裕を持ったものにすることができ、効率的な作業に繋がりコストの削減に繋がった。
H.試作品を作成してから量産する
いきなり量産に入ると、設計や仕様の問題が発生した場合大きな損失になります。先ず試作品を作成し、問題点を解消した後に量産することでリスクを軽減できます。また量産の可能性がある場合は事前にご相談頂ければ量産を前提とした加工やそれに対しての見積も可能となります。
半導体製造での具体的事例⑧・・・試作段階での設計見直し
量産前に試作品を作成し、装置への組み込みテストを実施したところ、一部の穴加工については穴の公差精度がラフで良いことが分かった。試作品なしで量産していた場合、無駄な加工費が発生していたが、事前に修正することでコストを削減。
I.加工業者と早い段階で相談する
設計段階からご相談頂く事で、加工上の課題を早期に発見し、コストを抑える設計やプロセスを採用できます。加工業者のアドバイスを受けることで不要な手間を省く事が可能です。弊社でも加工に関するご相談を承っております。
半導体製造での具体的事例⑨・・・設計段階での加工難易度の調整
製造装置の設計/開発段階で加工業者に相談したことにより、初期段階から低コストでの加工方法を検討することで結果として、加工コストの削減に成功。
J.長期的なパートナーシップを築く
信頼できる加工業者と長期的な関係を構築することで、価格交渉やお客様の個々の事情も知ることによりコスト削減が実現します。定期的な発注や情報共有を行うことで、互いにメリットが得られる関係を目指して下さい。
半導体製造での具体的事例⑩・・・定期発注による価格優遇/専用治具の開発
長年の取引実績により、一定数量以上の発注により価格が優遇されるようになり単価を削減。特定の製品に対し加工業者と協力して専用の治具を開発することにより、治具を用いることで加工精度が向上と、作業効率の向上により結果として年間でのコストの削減に成功。
4.受注側(加工業者)ができるコスト低減の方法
受注側でできる石英加工品のコスト低減の方法としては次のような事が考えられます。
- 加工工程の自動化
- 最適な工具の選定と管理
- 加工条件の最適化
- 端材やスクラップの再利用
- 作業プロセスの標準化
- 試作・設計支援サービスの提供
- 在庫管理の効率化
- 歩留まり率の向上
- エネルギー効率の改善
- 顧客ニーズに応じた柔軟な提案
これらについて説明していきます。
A.加工工程の自動化
CNC加工機や自動研磨機、自動溶接機、ロボットアームなどを導入し、手作業を減らすことで効率化を図り、時間と人件費を削減します。また、自動化により職人の属人化した作業を均一化し精度と安定性を向上させます。
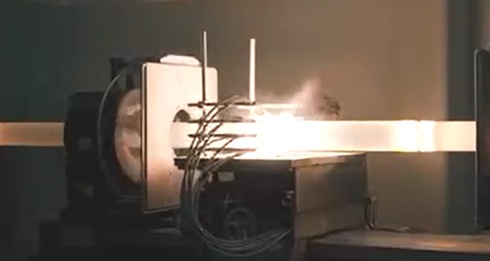

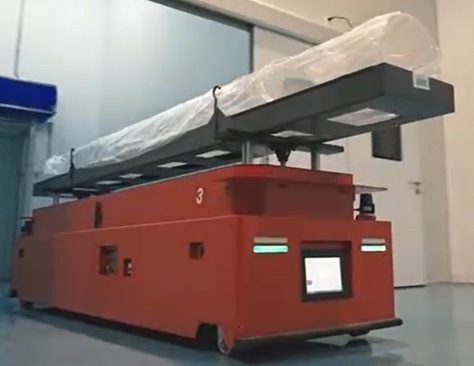
B.最適な工具の選定と管理
石英ガラス専用の高性能な工具(例:ダイヤモンド工具)を使用し加工時間を短縮させるとともに、工具の寿命を延ばすために適切なメンテナンスと交換タイミングを管理します。
C.加工条件の最適化
切削速度、研磨材の種類、温度管理など、加工条件を細かく最適化して歩留まりを向上させ、シミュレーション技術を活用して加工前に条件を検証する。
D.端材やスクラップの再利用
加工中に発生する端材やスクラップをリサイクルして材料コストを抑える。
E.作業プロセスの標準化
加工手順や品質検査の標準化を進め、作業員の熟練度の差による品質やコストのばらつきを低減させ、作業員のトレーニングを強化し生産性を向上させる。
F.試作・設計支援サービスの提供
顧客が設計段階で加工可能性を考慮できるように、試作支援や設計アドバイスを行い、無駄な工程や設計ミスを減らし製造効率を向上させる。
G.在庫管理の効率化
必要な材料を適量確保し在庫過多や不足を防ぎ、材料費や管理コストを削減するための需要予測のシステムなどの導入も検討していく。
H.歩留まり率の向上
最終製品については三次元測定機や投影機などを活用し品質検査を強化して不良品の発生を削減させ、工程途中では作業員の検査能力を向上させることで歩留まりを向上させる。
I.エネルギー効率の改善
加工機械や設備のエネルギー効率を改善し、電力やガス、研磨材などの使用量を削減させる。
J.顧客ニーズに応じた柔軟な提案
必要最低限の品質や加工精度で対応できる製品の提案を行い、コストを抑えた選択肢を提供し標準化された部品や規格品を提案することで加工費用を抑える。
4.まとめ
石英ガラス製品のコスト削減には、発注側(半導体メーカー・装置メーカーなど)と受注側(加工業者)が密接に連携し、設計・発注・加工の各プロセスを最適化することが不可欠です。
単に加工業者が努力するだけでは限界があり、発注側が設計段階で加工しやすい仕様を検討し、受注側と早期に協議することで、無駄なコストを抑えながら品質を確保することが可能となります。
発注側が公差の見直しや標準規格品の活用、発注ロットの最適化などの工夫を行い、受注側が生産プロセスの効率化や最新技術の活用を進めることで、双方にメリットのある関係を築くことができます。
そして何より重要なのは、「対話」と「継続的な改善」です。単発のコスト削減策ではなく、長期的な視点で改善を続けることで、品質とコストのバランスを最適化していくことが求められます。
特に、石英ガラスの価格高騰が進んでいる今、従来と同じ発注・加工の方法ではコスト増を抑えることが難しくなっています。材料(板、管、ロッド、ブロックなど)はメーカーから購入する必要があり、ここ1〜2年で50%以上の値上がりをしたものも珍しくありません。
また、溶接加工で使用する酸水素ガスや、アニール工程での電力消費コストも増加しており、加工業者の努力だけで吸収することは困難です。
こうしたコスト上昇に対応するため、加工業者側では自動化や生産プロセスの効率化、職人(作業者)の早期育成などに積極的に取り組んでいます。しかし、それだけでは不十分であり、発注側と受注側が一体となり、設計から生産までの最適化を進めることが、持続可能なコスト削減につながります。最適化についての具体的な進め方については、弊社でもご相談を承っております。
石英ガラスは高価な素材ですが、適切な設計・発注・加工のアプローチを取ることで、無駄を省き、効率的に製造することが可能です。本記事で紹介したポイントをご検討いただき、次回の発注時にぜひお役立てください。
最後までお読みいただき有難う御座いました。